核電建設(shè)中存在大量的預埋件焊接工程,因此預埋件的焊接合格率關(guān)系著核電建設(shè)的施工質(zhì)量和效率。為提質(zhì)增效降本,以科技創(chuàng)新助推核電高質(zhì)量建設(shè),中核二二鋼結(jié)構(gòu)分公司立足項目需求,成功研發(fā)自動埋弧螺柱焊設(shè)備。
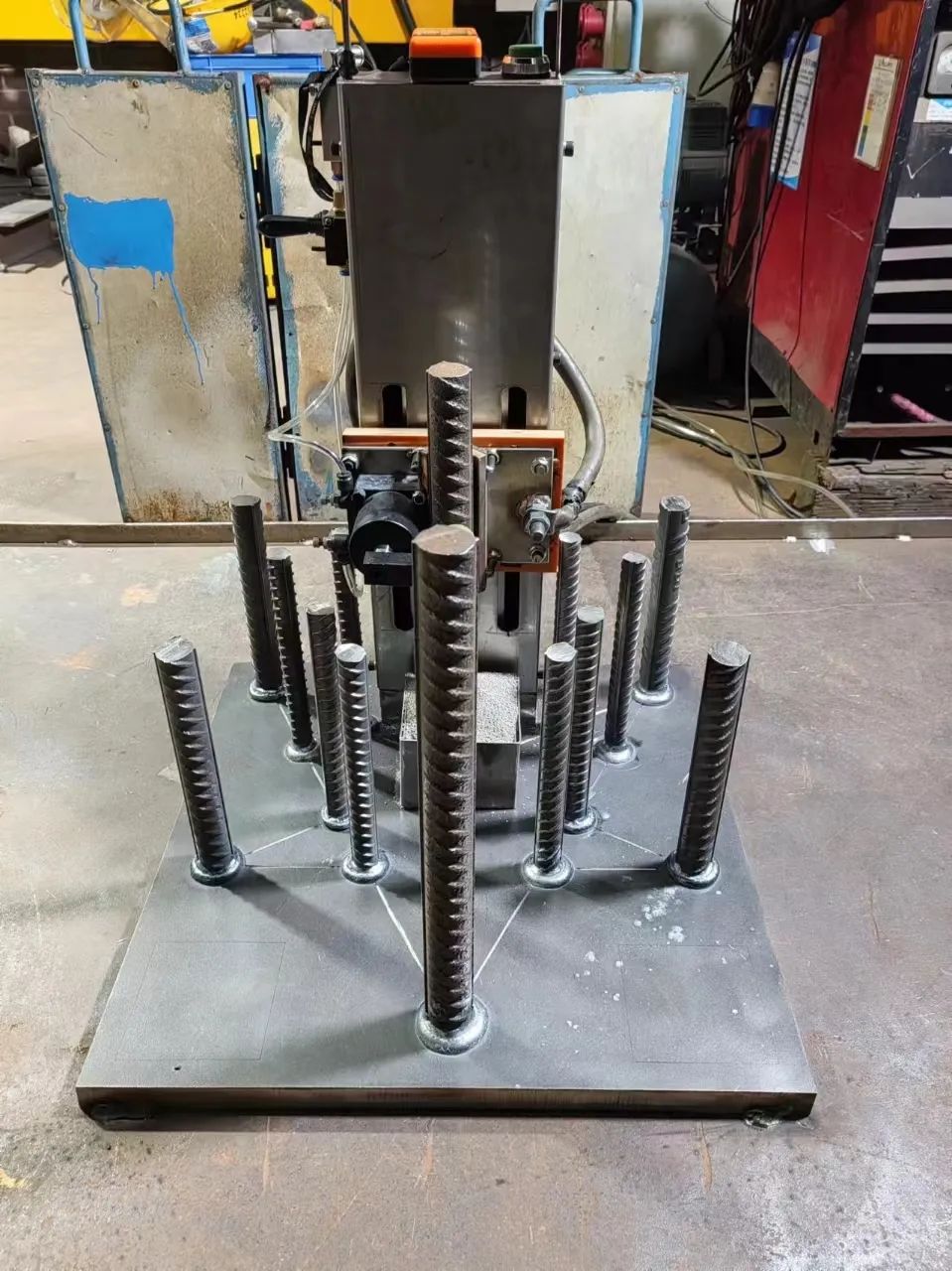
應(yīng)運而生,設(shè)備工藝向“新”升級
目前華龍一號、AP1000、CAP1000等系列核電堆型中存在著大量T型接頭的預埋件鋼筋,以往主要依靠焊工使用手工埋弧焊工藝完成鋼筋焊接,需要人工持續(xù)把持焊槍。在焊接過程中想要精確控制尺寸,保證焊接穩(wěn)定性、效率和一次合格率,對焊工的技能和經(jīng)驗要求較高。
因此,提升預埋件埋弧螺柱焊接效能成為迫在眉睫的任務(wù)。鋼結(jié)構(gòu)分公司成立專項研發(fā)團隊,在手工埋弧螺柱焊的基礎(chǔ)上研制出了自動埋弧螺柱焊設(shè)備。在焊接過程中,無需人工手持焊槍,操作簡單,大大降低了勞動強度,有效緩解了高級焊接技能人才短缺問題,同時實現(xiàn)了預埋件焊接過程自動化,一次合格率99%以上,無損檢測一次合格率100%,大大提高了預埋件焊接質(zhì)量。
厚積薄發(fā),焊接樣機向“優(yōu)”改進
研發(fā)過程中,鋼結(jié)構(gòu)分公司以公司技能大師工作室和焊接技術(shù)創(chuàng)新工作室為依托,成立青年黨員攻關(guān)團隊,以青年黨員骨干帶領(lǐng)研發(fā)團隊攻堅克難。
針對傳統(tǒng)手工埋弧螺柱焊使用中出現(xiàn)的問題,團隊開展了自動埋弧焊接設(shè)備的原型設(shè)計,它主要由控制系統(tǒng)、焊接電源、埋弧螺柱焊槍三部分組成。其中,針對焊接電源的選擇,團隊對3種不同品牌型號焊接電源分別從便攜性、經(jīng)濟性、穩(wěn)定性以及焊接電流適用性等4個方面進行了詳細的對比實驗,最終選擇了現(xiàn)有的埋弧焊接電源,可降低設(shè)備整體成本。
鋼筋夾持是設(shè)備研發(fā)過程中的重中之重,團隊對機械、氣動、電動3種鋼筋夾持方式進行反復對比分析,不斷試驗和優(yōu)化夾持工裝結(jié)構(gòu),最終成功研發(fā)了結(jié)構(gòu)簡單、易維護、夾持力度大且穩(wěn)定的氣動自動夾持工具。
另外,團隊還開發(fā)了埋弧螺柱焊接系統(tǒng),采用伺服電機驅(qū)動的方式,通過系統(tǒng)可精確控制鋼筋的提升、下壓、起弧等參數(shù),可根據(jù)不同鋼筋的焊接需求,直接在控制系統(tǒng)上設(shè)置和選擇焊接參數(shù),無需人員參與。在團隊長達半年的努力下,于2023年3月成功研發(fā)出了第一代原型樣機。
此后,團隊加快樣機優(yōu)化與系統(tǒng)升級進度。采用快速接口解決了線纜凌亂問題,通過無線控制器實現(xiàn)電磁自動吸附,并配上一體式的不銹鋼外殼;尤其是對于大直徑鋼筋的焊接,通過優(yōu)化系統(tǒng)增加鋼筋提升速度與時間,解決了焊接起弧異常和外觀成形一致性較差的問題。同時,團隊對設(shè)備穩(wěn)定性進行了批量測試,各項檢測指標均滿足標準要求,一次合格率99%以上。歷時3個月反復測試,成功研發(fā)出顏值與性能兼具的第二代設(shè)備,實現(xiàn)了可產(chǎn)品化制造。目前已獲2項專利授權(quán),具有自主知識產(chǎn)權(quán)。
順勢而為,焊接設(shè)備向“廣”應(yīng)用
目前,第二代設(shè)備已在三門核電二期3號機組鋼穹頂制作鋼筋全熔透焊縫焊接中推廣應(yīng)用,完成了2000余根鋼筋焊接,焊接性能穩(wěn)定,焊縫成形美觀,焊后無需打磨,節(jié)省了大量的打磨時間。
同時,該設(shè)備具有良好的經(jīng)濟效益,相比于傳統(tǒng)手工埋弧螺柱焊和手工氣保焊,自動埋弧螺柱焊可顯著節(jié)約施工成本,且具有廣泛的應(yīng)用前景。
下一步,中核二二鋼結(jié)構(gòu)分公司將繼續(xù)堅持推動焊接技術(shù)的創(chuàng)新研發(fā),加快形成新質(zhì)生產(chǎn)力,助力核電工程高質(zhì)量建設(shè)。